High speed stamping machine require regular maintenance to ensure their stable operation and extend their service life. Regular maintenance can effectively prevent mechanical failures and improve the reliability and production efficiency of equipment. Generally speaking, the maintenance frequency and specific steps can be determined according to the frequency of use of the punching machine, the working environment and the manufacturer's recommendations, but general maintenance includes the following aspects:
Cleaning and lubrication: Regularly clean the various parts of the punching machine, especially the punch, guide rails and transmission parts, to prevent dust and debris from affecting its operation. At the same time, ensure that the lubrication system operates normally and that the lubrication effect of each moving part is good.
Inspection and adjustment: Regularly check the various parts and connectors of the punching machine to ensure that there are no loose or severely worn areas. Make adjustments when necessary, such as the centering adjustment of the punch, to ensure the accuracy and stability of the punching machine.
Replace wearing parts: Regularly replace wearing parts such as dies, guide rails, springs, etc. according to usage and manufacturer's recommendations. These parts may wear or age due to long-term use, and timely replacement can avoid equipment failures and downtime caused by them.
Safety inspection: Regularly check whether the safety devices and protective measures of the punching machine are intact and effective to ensure the safety of the operator.
Record maintenance information: Establish and maintain maintenance records, record the time, content and maintenance personnel of each maintenance. These records help to detect potential problems in time and perform preventive maintenance.
Regular maintenance is an important measure to ensure the normal operation and extend the service life of high speed stamping machine.
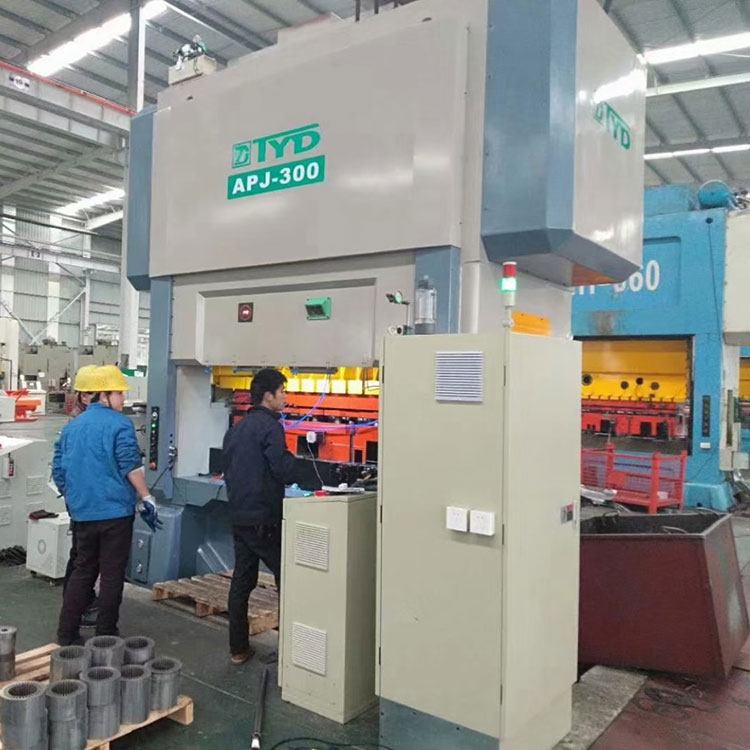